de Infinite
Infinite,
jouw kennispartner
voor simulatie oplossingen.
Met de geavanceerde simulatieoplossingen van Ansys helpt Infinite je de kwaliteit van jouw producten te verbeteren, kosten te verlagen en de time-to-market te verkorten.
Bekijk onze oplossingen Over ons
de Infinite
Onze simulation values
Ontdek meer30%
time-to-market
2 jaar
cyclustijden
66%
nieuwe product rollouts
In welke sector werk jij?
Lucht- en ruimtevaart
Ansys simulatietools spelen een cruciale rol bij het waarborgen van de veiligheid, betrouwbaarheid en prestaties van luchtvaartsystemen en -componenten tijdens het ontwerp- en ontwikkelingsproces.
Automotive
Om concurrerend te blijven in de auto-industrie moeten engineeringteams zo snel mogelijk kwalitatief hoogwaardige onderdelen leveren. Een belangrijk element in het verkorten van de ontwikkelingstijd is engineering simulatie waarmee bedrijven ontwerpen kunnen itereren om snel aan de productvereisten te voldoen.
Defensie
Ansys simulatiesoftware wordt gebruikt om het moderniseringsproces te versnellen en militaire technologie te verbeteren door defensie organisaties in staat te stellen strategieën en technologieën in een gecontroleerde omgeving te testen en te verfijnen voordat ze in echte scenario's worden ingezet.
Gezondheidszorg
Het ontwerpen en verkrijgen van reglementaire goedkeuring voor complexe oplossingen in de gezondheidszorg kan duur en tijdrovend zijn. De Ansys simulatiesoftware biedt doeltreffende oplossingen om deze uitdagingen aan te gaan. Door deze in silico benadering te gebruiken, kan de veiligheid van de patiënt worden gemaximaliseerd terwijl de gezondheidszorg betaalbaarder wordt.
Energie
De overgang naar een duurzamere energiesector verloopt snel. De simulatieoplossingen van Ansys spelen een sleutelrol in de versnelde ontwikkeling van koolstofarme technologieën en verbeteren tegelijk de productiviteit, betrouwbaarheid, veiligheid en milieu-impact van traditionele energiebronnen.
High Tech
Om overeind te blijven, moeten bedrijven in de hightechsector wendbaar en innovatief zijn. Dit kan worden bereikt door digitale transformatie met behulp van simulatie, die efficiëntere innovatie mogelijk maakt terwijl het verbruik van middelen en de bijbehorende kosten worden geminimaliseerd.
Industriële apparatuur
Simulatie is een van de belangrijkste sleutels tot het ontsluiten van het volledige potentieel van Industrie 4.0. Het stelt productieorganisaties in staat om concepten voor de productlevenscyclus virtueel te valideren - van het identificeren van problemen tot het verminderen van het aantal ongevallen en nog veel meer.
Offshore en scheepvaart
De offshore- en scheepvaartindustrie gebruiken Ansys-simulatieoplossingen om de impact van milieubelastingen te begrijpen, potentiële structurele zwakheden te identificeren en de efficiëntie en veiligheid te verbeteren terwijl ze hun producten op een rendabele en duurzame manier leveren.
Specifieke vragen?
Spotlight op
Electronics
Onze electronics-oplossingen helpen je bij het oplossen van elektromagnetische, temperatuur-, SI-, PI-, parasitaire, bekabelings- en trillingsproblemen! Het stelt je in staat om je ontwerp volledig te simuleren en de vragen die je hebt op te lossen. Onze experts staan klaar om je alles te vertellen over de mogelijkheden die deze software je biedt.
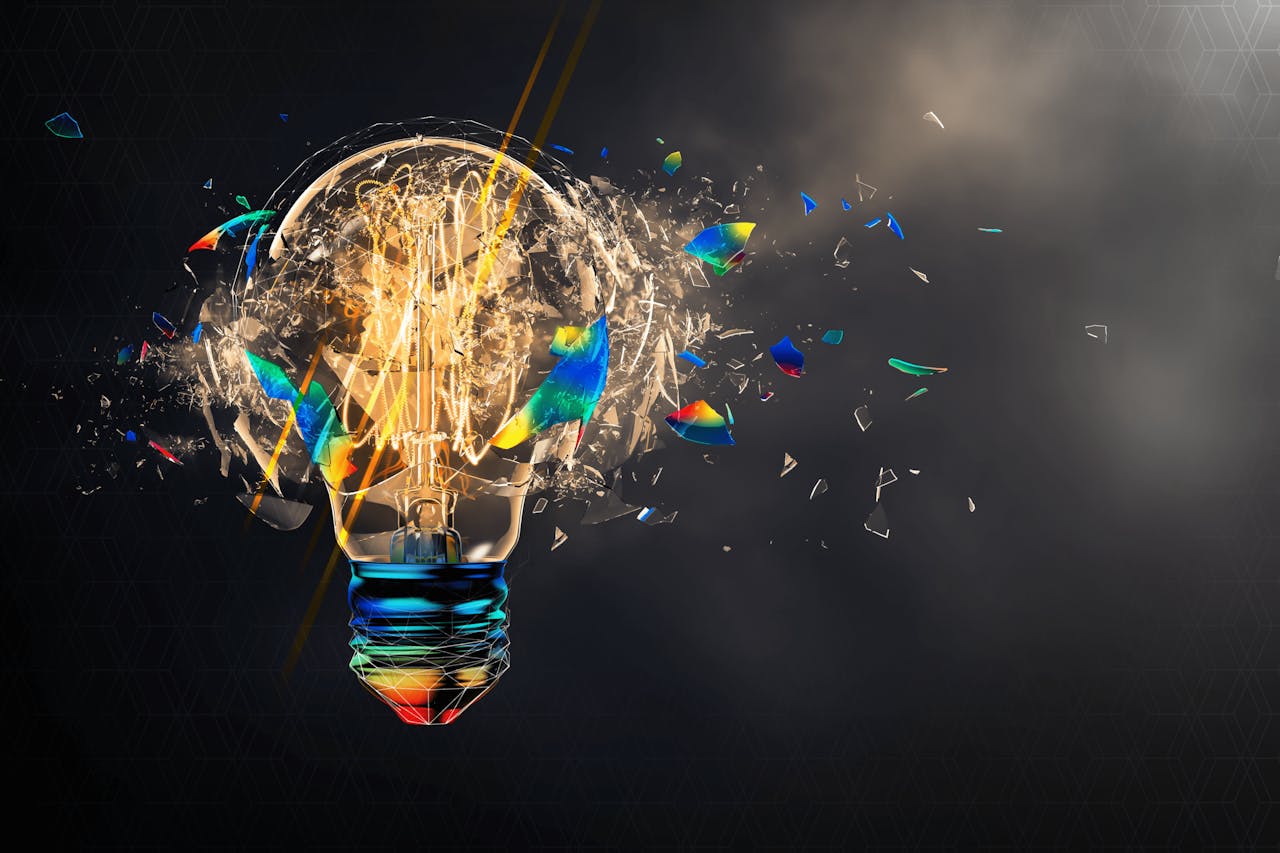
Ansys solutions
Geïnteresseerd? Neem contact met ons op voor de mogelijkheden.
Onze opleidingen
april 2024
dinsdag
duur: 1 dag
Ansys Discovery Modeling
maandag
duur: 2 dagen
Introductie Ansys Maxwell
Onze laatste blogs
Infinite is een van de Ansys Elite Channel Partners
Dit wil zeggen dat we gecertificeerd zijn om Ansys oplossingen te verkopen en jou te helpen met al je vragen. Om ‘Elite’ partner te zijn, moeten we voldoen aan strenge voorwaardes zodat we jou altijd zo goed mogelijk kunnen helpen. Een van die voorwaardes is bijvoorbeeld dat onze sales én support elk jaar een opleiding volgen om te zorgen dat we altijd op de hoogte zijn van de laatste ontwikkelingen!
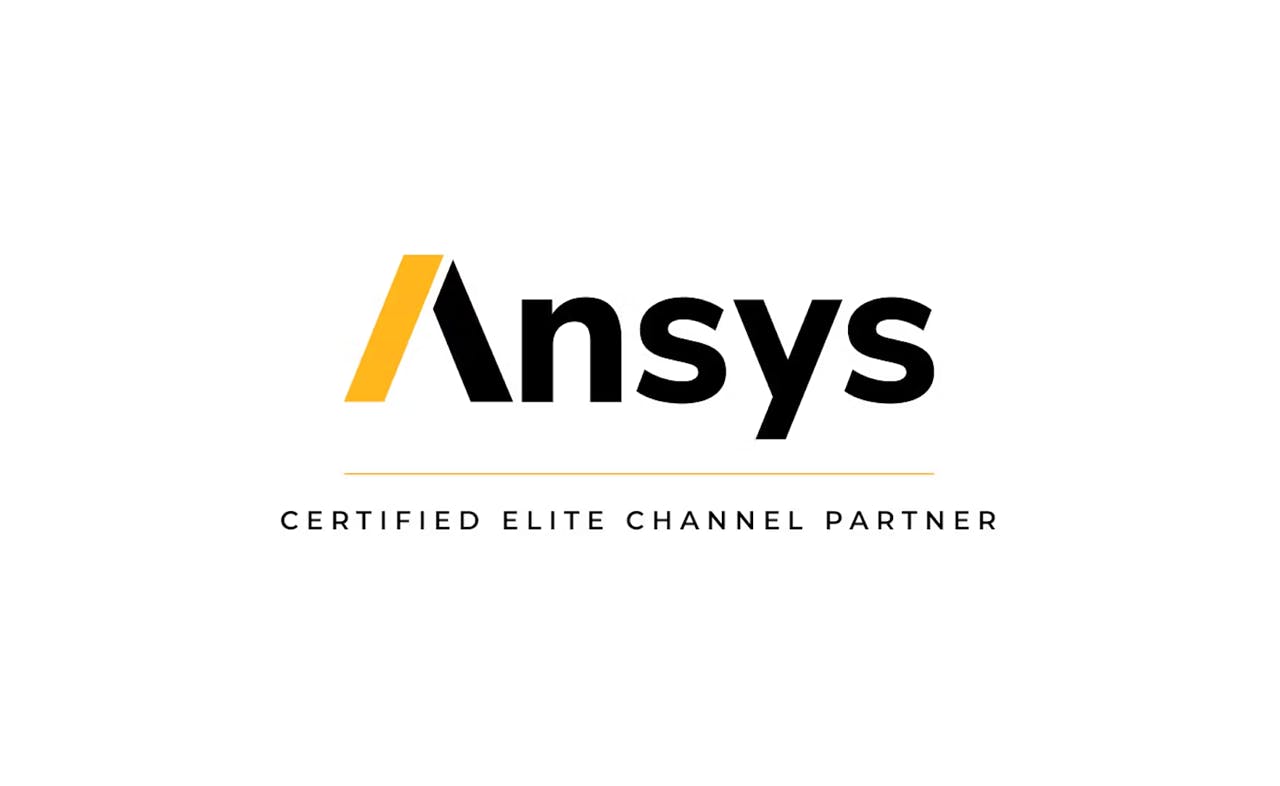